In the world of fluid control, two types of valves stand out for their functionality and versatility: ball valves and globe valves. While both serve essential roles in managing the flow of liquids and gases, they operate differently and are suited for various applications. Understanding the distinctions between these two types of valves can help engineers, designers, and facility managers make informed decisions for their specific needs. In this article, we will explore the characteristics, advantages, and applications of both
ball valves and globe valves, helping you choose the right valve for your system.
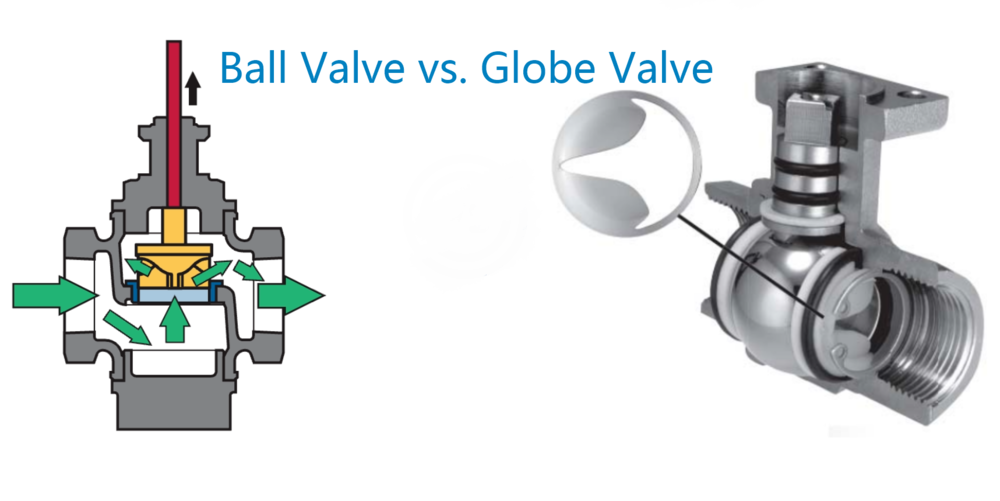
A globe valve is a type of valve that features a linear travel plug, which fits into a seat enclosed within a spherical body—hence the name "globe valve." The design allows for precise control of fluid flow through the valve. By moving the plug up or down in relation to the seat, operators can regulate the flow. When fully closed, the plug creates a tight seal, stopping the flow of fluid.
Globe valves are primarily used in applications where precise flow control is necessary. They excel in regulating, throttling, or isolating flow, making them a popular choice in heating, ventilation, and air conditioning (HVAC) systems. Common applications include hot water heating systems, steam systems, and chillers, where modulating flow is critical for optimal system performance. Their design allows for efficient flow management, even under varying pressure conditions.
The linear motion of the plug allows for fine adjustments, making globe valves ideal for applications requiring careful regulation.
Globe valves are particularly effective in throttling applications, enabling partial flow control.
When fully closed, globe valves provide excellent sealing capabilities, reducing the risk of leaks.
They can be used in a variety of applications, from residential plumbing to large industrial systems.
A ball valve is another popular type of valve used for controlling fluid flow. It features a rotary ball with a hole running through its center. When the valve is open, the hole aligns with the pipeline, allowing fluid to flow through. Conversely, when the valve is closed, the hole is perpendicular to the flow direction, effectively stopping the passage of fluid. The operation of a ball valve is straightforward, relying on the rotation of the ball to increase or decrease the flow.
Ball valves are known for their speed and ease of operation. They can be opened or closed with a simple quarter turn, making them ideal for applications where rapid shutoff is necessary. This design also minimizes pressure drop, making ball valves highly efficient for on/off control of fluid flow.
Ball valves can be opened or closed with just a quarter turn, allowing for fast and efficient flow control.
Their design minimizes resistance to flow, resulting in lower pressure loss through the valve.
Ball valves are built to withstand high pressures and temperatures, making them suitable for demanding applications.
When closed, ball valves create a tight seal, preventing leaks and ensuring system integrity.
While both ball valves and globe valves serve the purpose of controlling fluid flow, several key differences set them apart:
Operate using a linear motion plug to control flow. The design allows for precise adjustments but can result in higher pressure drops when partially open.
Utilize a rotary ball mechanism for on/off control, offering quick operation with minimal pressure loss.
Ideal for applications requiring precise flow regulation and throttling, such as in HVAC systems.
Best suited for applications needing fast shutoff or simple on/off control without the need for throttling.
Typically have a higher pressure drop due to their design and the way they restrict flow.
Have a lower pressure drop, making them more efficient for applications where maintaining pressure is critical.
Commonly found in heating systems, chillers, and situations requiring precise control over fluid flow.
Often used in oil and gas, water supply, and chemical processing for quick shutoff applications
Selecting the right valve for your application depends on several factors:
Consider whether your application requires precise flow control or quick shutoff. If modulation and throttling are necessary, a globe valve may be the better choice. For straightforward on/off control, a ball valve is more suitable.
Evaluate the pressure and temperature conditions of your system. Both valve types can handle high pressures and temperatures, but ball valves often perform better in high-pressure scenarios due to their robust construction.
Consider the physical space available for installation. Ball valves are generally more compact, while globe valves may require more space due to their design.
Globe valves can be more expensive than ball valves due to their complex design. Consider your budget and the long-term value of each option.
In summary, both ball valves and globe valves have distinct advantages and specific applications that make them valuable in fluid control systems. Ball valves are ideal for quick shutoff and low-pressure drop scenarios, while globe valves excel in applications that require precise flow regulation. By understanding the key differences between these two types of valves, you can make informed decisions that optimize the performance of your fluid systems. Whether you need the fast operation of a ball valve or the precise control of a globe valve, choosing the right valve is essential for ensuring the efficiency and reliability of your operations.