A pressurized water reactor nuclear power plant equipped with two million-kilowatt units is a relatively common and reasonable, which consists of NI (Nuclear Islands), CI (Conventional Islands) and power plant auxiliary facilities, and the nuclear island includes the nuclear steam supply system (NSSS) and the nuclear island auxiliary facility. NI is the core of the nuclear power plant, where nuclear energy is converted into thermal energy and a large amount of steam is produced to provide power generation. CI is the main force of the nuclear power plant, where heat energy is converted into electrical energy (including the whole process from steam turbine power generation to power output). Although the nuclear island auxiliary facility is not the main part, it is also indispensable, just like the screws on the equipment. Among the nearly 30,000 valves, valves in NI account for 43.5%, CI 45%, and the nuclear island auxiliary facility 11.5%. Valves are used more for CI. Compared with thermal power unit valves of the same level, it is characterized by larger diameters, and the pressure and temperature are not too high. Therefore, from a technical point of view, the technical difficulty of CI valves is relatively lower than that of NI valves. The valves used for the nuclear island auxiliary facility are not many, and the technical difficulty is lower. Some NI valves are introduced in this article.
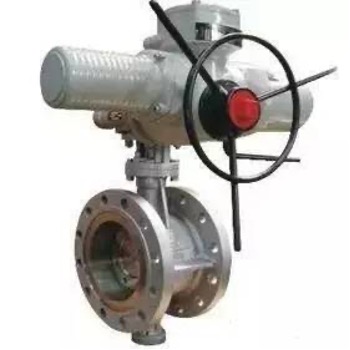
Figure 1 Pneumatic wafer butterfly valves
According to the type of valves, NI valves mainly include gate valves, globe valves, check valves, ball valves, butterfly valves, safety valves, pressure reducing valves, steam traps and regulating valves. According to the proportion of the used amount globe valves account for 33.6%, ball valves 12.8%, check valves 7.2%, butterfly valves 5.7%, gate valves 5.0%, and 3.5% regulating valves, safety valves 2.5%, steam traps 0.3%, pressure reducing valves 0.2%, and other valves 3%. According to the nuclear safety level, valves can be divided into nuclear levels 1, 2 and 3 and non-nuclear level, accounting for about 2.3%, 30%, 22% and 45.7% of the total number of NI valves.
The description of nuclear power valves
Maximum diameter for nuclear level 3 butterfly valve: 1200mm
Maximum diameter for nuclear level 2 main steam isolation valve: 800mm
Maximum diameter for nuclear level 1 main circuit gate valve: 350mm
The highest pressure: 1500 LB
The highest temperature: 350℃
Medium: coolant (bored water)
There are about 1.13 million valves for NI in nuclear power plants, with various varieties and specifications. Only several valves for nuclear power plants are introduced.
Globe valves
Nuclear grade globe valves usually have three structures, packing globe valves, bellows globe valves and metal diaphragm globe valves. The diameter of the
globe valve in NI is generally less than 50mm, and a small amount reaches 80mm. Most of the globe valve body is formed by die forging, and the inlet and outlet flow channels need to be designed as straight holes with slopes processed by machining, so the fluid resistance is relatively great. The driving methods are generally manual and pneumatic, and the accuracy of stroke and torque control must be considered when using the electric type. The packing globe valve adopts a double packing structure with disc spring loading. There are two types of connection between the valve body and the bonnet: flanges and threads, and lip sealing welding should be provided. The bellows globe valve uses bellows as the first seal to ensure no external leakage, and is equipped with a stuffing box to prevent the valve from working temporarily once the bellows is damaged, so as not to make the accident more serious. The bellows should be at least double-layered, and three or even multi-layered should be used for high pressure. The metal diaphragm globe valve uses a metal diaphragm as a seal to isolate the valve stem from the inner cavity. It is often designed as a Y-shaped structure in terms of body shape to reduce its fluid resistance. However, the opening of this valve should not be too big, otherwise, it will have adverse consequences on the fatigue and service life of the diaphragm.
Globe valves are mainly used in auxiliary pipelines. The medium is water and steam. The nominal diameter is DN10 to DN350, and the nominal pressure is 17.2MPa; the working temperature is 371°C, and the globe valve is mostly bellows sealed and welded.
Butterfly valves
Nuclear-grade butterfly valves usually have three structures, coaxial direct-connected rubber-lined butterfly valves, eccentric metal-sealed butterfly valves and double-acting metal-seated butterfly valves. The diameter of the butterfly valve in NI is from DN50 to DN1200. Among them, the coaxial direct-connected rubber-lined butterfly valve is mostly used in the system for conveying cooling water, raw water and desalinated water in BNI. Because the rubber soft seal is used, the pressure is lower than 150LB. The nuclear level is generally 3. The upper handle, worm gear pair, pneumatic device or electric device can realize the opening and closing or adjustment of the valve. Metal-seated butterfly valves are often used in systems that transport air in containment vessels. The butterfly valve with eccentric structure is closed by contacting and pressing the sealing surface of the valve body when the butterfly plate rotates to the maximum eccentric distance. The sealing surface is easy to be worn due to the relative friction, and the requirements for processing size control are also high. The structure of the double-acting butterfly valve is to use the cam mechanism to make the butterfly plate not be in contact with the sealing surface of the valve body before turning, and then turn 90°. At the same time, the sealing surface on the valve plate is made from a special metal with an inner support O-ring, with self-sealing, and a pneumatic device with spring return, which can reliably realize the function of emergency cut off or discharge of the medium.
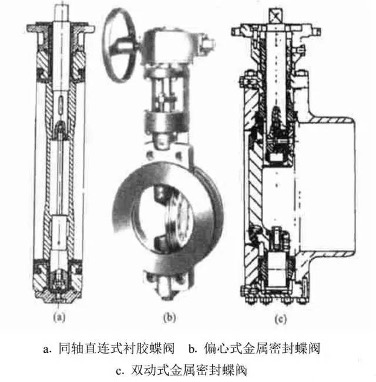
a. Coaxial direct connection rubber-lined butterfly valves b. Eccentric metal seated butterfly valves c. Double-acting metal seated butterfly valves
Figure 2 Several butterfly valve structures
Butterfly valves are mainly used in the cooling system of nuclear power plants. The nominal pressure is below 0.3 to 2.5MPa. The working temperature is 100 to 150℃, and the nominal diameter is 80 to 5500mm. The quick-closing butterfly valve is used in the air duct system, with a nominal diameter of 400 to 1200mm.
Ball valves
Ball valves have a nominal diameter of 6 to 350mm, nominal pressure 1.0 to 14.5MPa, and working temperature 196 to 500℃. This valve accounts for about 12.8% of the total number of valves used in the nuclear island system.
Check valves
Nuclear check valves mainly have three structures, swing check valves, lift check valves and double-plate check valves. The check valves used in NI are mainly swing check valves and lift check valves. The diameter of the swing check valve is generally above 80mm, corresponding to the gate valve. Its structural feature is that the pin shaft of the rocker is built-in and fixed in the valve body, which is mainly to eliminate possible leakage. The diameter of the lift check valve is generally below 50mm, corresponding to the globe valve. Its structure is divided into two types, that is, without spring and with spring. The two structures have their advantages and disadvantages. The structure with a spring is reliable in resetting and can return to the seat in time. However, under the working condition of small pressure difference, the valve disc will not open properly and affect the flow rate due to the great flow resistance and increased energy consumption. The structure without spring is simple, but it is easy to cause jamming and not reset. Therefore, attention must be paid to the fit clearance and guide length between the disc and the inner hole of the valve bonnet, and suitable material must be paid attention to. For the double-plate check valve flange, the two semicircular valve plates are reset by the control of the torsion spring. When it is opened, the medium pushes the valve plate back to the central axis and leans against the central axis, forming an included angle, and the fluid resistance is smaller than that of the swing check valve and the lift check valve. The diameter of this valve is relatively big, ranging from DN50 to 700mm.
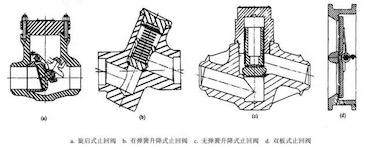
a. Swing check valves b. Lifting check valves with springs c. Lifting check valves without springs d. double plate check valves